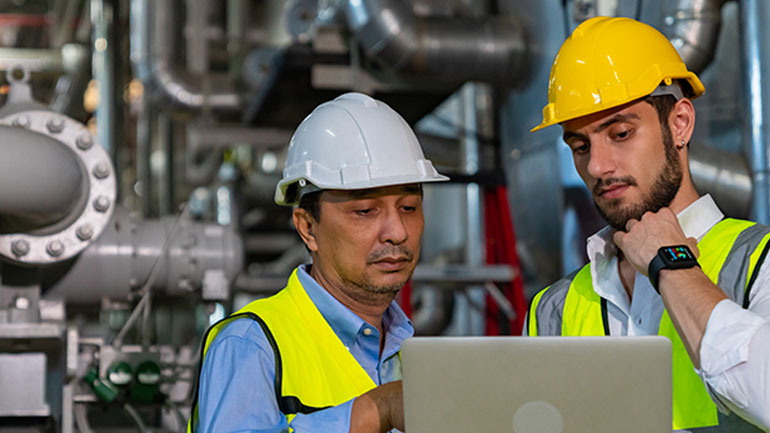
Plant outages, though seemingly disruptive, are essential for maintaining peak plant performance and preventing unnecessary and unplanned downtime. They provide an opportunity to assess equipment, conduct scheduled repairs, and optimize plant operations. A critical component of this is the post-outage report, which serves as a valuable tool for evaluating the outage’s effectiveness, identifying issues for improvement, and informing future maintenance strategies.
A comprehensive post-outage report captures crucial information that guides maintenance decision-making and enhances future outage planning. It encompasses:
- Overall outage performance assessment – Evaluating the effectiveness of the outage strategy, identifying areas of success, and pinpointing areas for improvement.
- Benchmarking for maintenance and reliability comparisons – Establishing benchmark data for maintenance and reliability metrics, enabling comparisons with industry standards and historical performance.
- Documentation updates – Updating plant documentation with the latest maintenance information and recommendations, ensuring accurate and up-to-date records.
To maximize the value of post-outage assessments, four important KPIs should be tracked:
Zero safety incidents
The goal for all plants is to have zero safety incidents, and planned maintenance events should be no exception. Any safety incidents during an outage should be thoroughly investigated and implement preventive measures for future outages as ensuring employee safety is key to the long-term success of any operation.
On-time schedule completion
Adhering to outage schedules is critical to minimize downtime and maximize uptime. Depending on the variety of assets to be checked, maintenance completion time may vary. Analyzing previous outage data helps to identify maintenance priorities and refine planning for future outages.
Initial scope quote remains within budget
Outages involve both production loss and maintenance costs, which is why keeping expenses within the initial scope is important. Scope growth may occur, so documenting all expenses and obtaining the proper approvals for additional costs is necessary to ensure transparency and accountability.
Successful startup with zero quality issues
A successful outage extends beyond on-time completion and meeting specifications – it culminates in smooth start up with no quality issues. Working with an Emerson Accredited Service Provider ensures access to certified technicians who prioritize quality, health, safety, and environmental (QHSE) standards, safeguarding your assets and personnel.
Effective outage management and post-outage reporting are cornerstones of plant optimization. Leverage NECI’s expertise in shutdowns, turnarounds, & outages to ensure peak performance, minimize downtime, and enhance overall reliability. Get in touch with one of our Experts 24/7/356 at 1-844-NECI-NOW or contact us to learn more.